產品說明
開發案例為MicroSD連接器,如圖1所示,產品尺寸長約15.3 mm、寬約14.1 mm、高約1.6 mm,模穴體積+流道體積約1.6cc。此案例採用一模四穴方式,有2種不同的流道與澆口設計(如圖2、圖3所示)。
使用材料
本案例所採用的材料為LCP SOLVAY XYDAR MG-350,含纖量30%。
案例解析
本案例以Moldex3D 黏彈性模組進行充填、保壓的殘留應力分析,以及利用翹曲模組進行翹曲變形的預測,提供一組在殘留應力分布與最小翹曲量值的最佳設計方案。
問題焦點:
進澆口設計對於殘留應力分布的影響性
進澆口設計對於翹曲變形量值的影響性
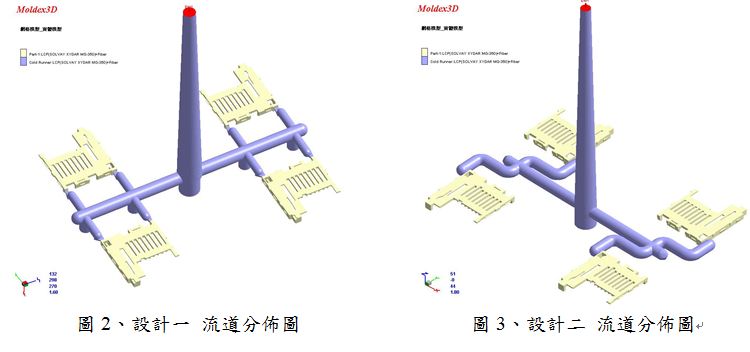
分析設計一
設計一為兩點進澆設計採魚骨型流道設計(流道體積約為1.62cm3),從Moldex3D分析之流動等位線結果如圖4,在等位線較密集的地方會產生結合線,模穴內Von Mises應力分佈如圖6,其最大預測分布值約為0.8MPa。當保壓結束時,模穴內的最大剪切應力如圖8,其值約為0.4MPa。
圖10為保壓結束時,模穴內的溫度剖面圖。
一般而言,射出成形製程中在充填流動時會對於高分子鍵結產生主要應力因此最大的主軸應力(Principal stress)會與Von Mises應力接近;而最大的剪切應力約為Von Mises應力的一半。圖12為總位移量分佈圖,包含產品因體積收縮率或殘留應力所造成之總位移,其值從0.001mm~0.13mm。
分析設計二
設計二為兩點進澆設計採單點進澆流道轉折設計以緩衝塑料流速避免產生噴流與表面流痕的缺陷(流道體積約為1.29cm3),Moldex3D分析之流動等位線結果如圖5,其結合線位置與設計一接近;從Moldex3D分析當保壓結束時,模穴內Von Mises應力分佈如圖7,其最大分布值約為1.0MPa。圖9為保壓結束時,模穴內的最大剪切應力,其值約為0.5MPa。圖11為保壓結束時,模穴內的溫度剖面圖。圖13為總位移量分佈圖,包含產品因體積收縮率或殘留應力所造成之總位移,其值從0.001mm~0.12mm。我們發現與設計一的量值接近,翹曲的最大量值分佈皆在本設計工件兩側的地方。
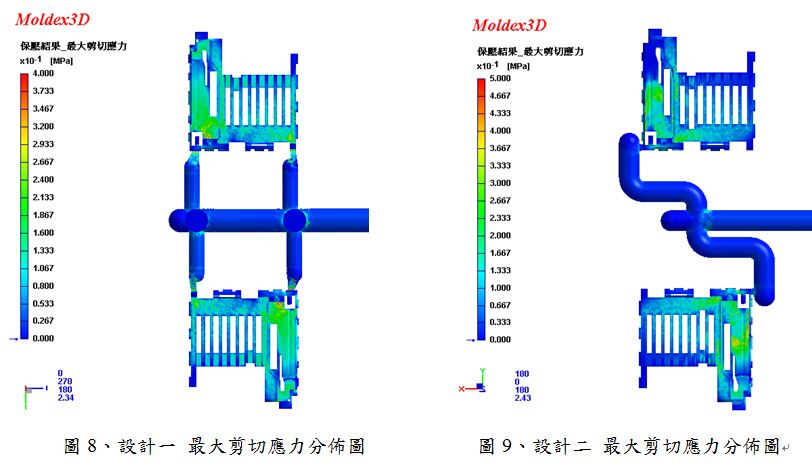
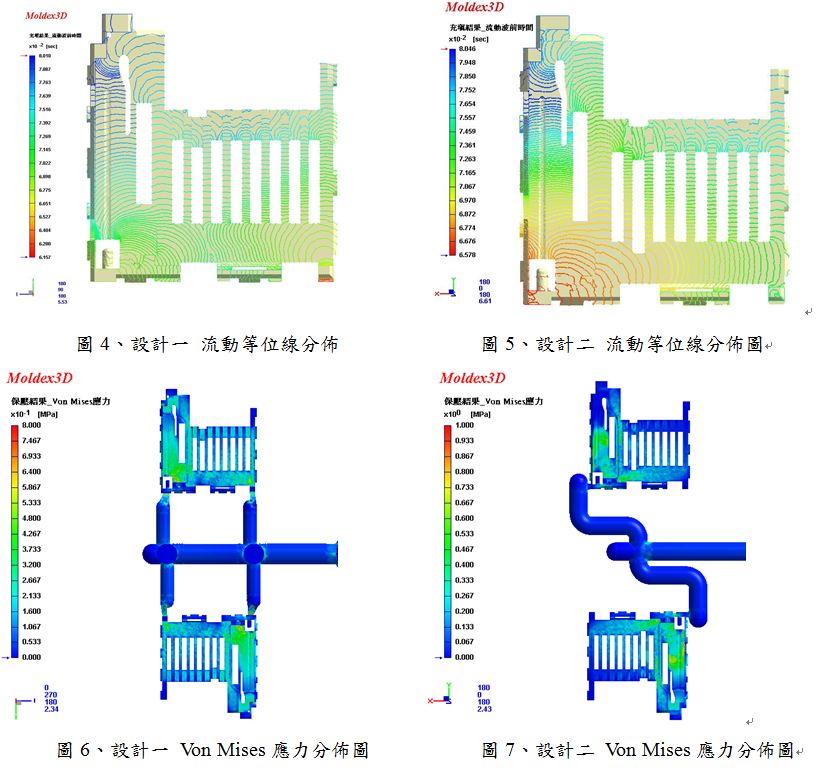
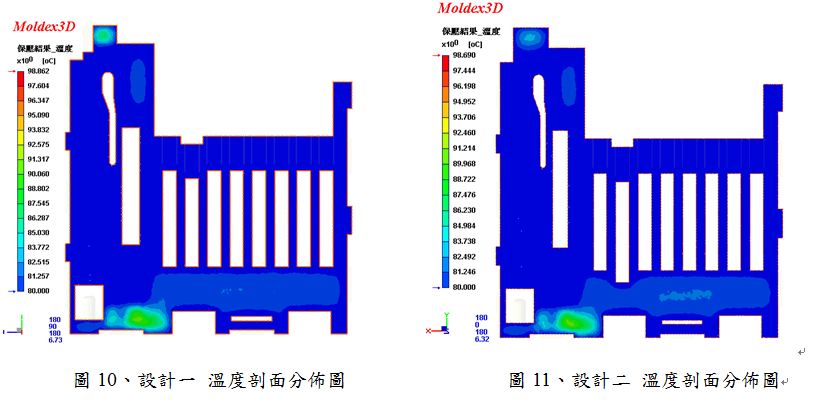
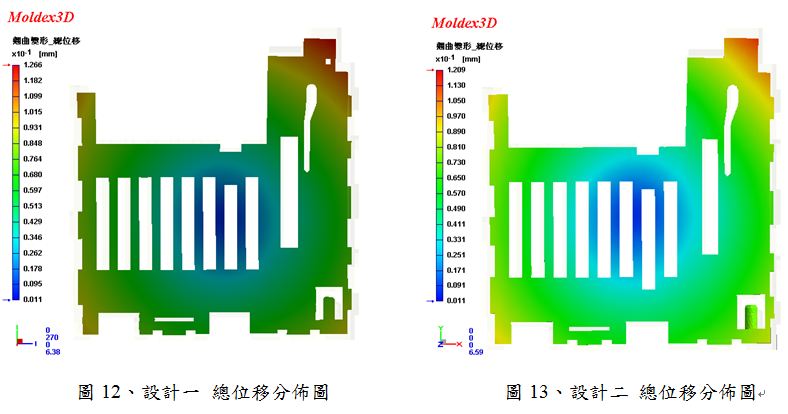
結論
殘留應力(residual stress)為塑膠材料成品在經過製造或成形過程後,在無外力作用下或無溫度梯度存在時,物體內部仍維持應力之狀況。射出成形過程中產生殘留應力的有兩種:
1. 流動應力的形成─當熔膠經高壓快速充填時,高剪切作用造成分子鏈高度定向,此是造成殘留應力之主因。
2. 熱應力的形成─當成品溫度快速冷卻到塑膠的 Tg 以下時,冷卻收縮造成之分子鏈間應力無法完全釋放。
當塑件內的應力在外界提供相當的能量時(如過SMT)被釋放開後,塑件可以自由地收縮與變形。因此造成塑件收縮和翹曲的主要因素是殘留應力。透過本案例的兩個設計方案,從結果發現兩組不同澆口設計所預測的翹曲量值接近,但藉由Moldex3D黏彈模組分析結果可以得知設計一的殘留應力分布較設計二為少如此可降低在過SMT時因應力釋放產生高的翹曲量值。 |